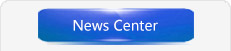
- What is the market p...2025/4/21
- Breakthroughs in the...2025/4/21
- A delegation of youn...2025/4/15
- Polypropylene fine d...2025/4/14
- Opportunities and ch...2025/4/14
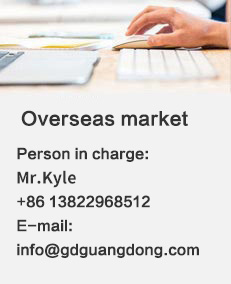
"Talent-based" is one of the five basic principles of the "Made in China 2025" plan. According to the report of the China Textile Industry Federation in the spring of 2018, textile intelligent manufacturing represented by new technologies such as big data, internet of things and artificial intelligence, and ecological brands represented by cultural creativity, fashion media, brand marketing, etc. The new economy, represented by the sharing economy, platform economy, and personalized customization, has continuously increased the demand for innovative talents in various industries.
Applicable talent is scarce
At present, the employment of the textile and garment industry has brought three extremely prominent problems: First, it is difficult to recruit workers, and the mobility of workers is large; Second, the average age of workers and staff members is generally higher, and there are faults between generations, and “85” workers are becoming increasingly scarce; Third, there are problems such as high-end design and R&D talents and advanced marketing management talents that are difficult to introduce and difficult to retain.
For example, in Jiangxi Qingshanhu District, the labor force in the textile industry needs 80,000 people. Currently, the actual labor force is only 60,000, and the labor shortage is 20,000. Hunan Huarong Textile and Garment Enterprises lacked first-line workers such as machine repairs and block cars. The current industry development of Xiantao in Hubei still faces the problems of old age and difficult recruitment. Local enterprises in Wuxi reported that the mobility of front-line employees has increased, and the recruitment of enterprises in Wuxi has been declining year by year.
Not only in these areas, including the southeastern coastal areas such as Fujian and Guangdong, but also in the central and western regions of Shaanxi, Xinjiang, and other places, there is a prevailing perception of society in the textile and clothing industry, as well as the alienation of employment concepts of the new generation of employed people, which makes the textile and clothing industry a talent shortage. Gradually increase. In addition, the new generation of employed population also puts forward higher requirements for the supporting facilities of the employment place, and it is relatively easy for enterprises near the urban core area to recruit workers.
At the same time, many industrial enterprises in Fujian and other places are facing the problem of “secondary succession” and face challenges in changing management models and selecting managers.
Slightly different from other provinces, Anhui and Jiangxi are traditionally the major provinces exporting labor to developed coastal regions. In recent years, the population migration has entered a new era of “outgoing population return”.
According to data from the Anhui Bureau of Statistics, by 2017, it has been returning for five years. A sample survey of the changes in the province's population in 2017 showed that the number of outbound residents in Anhui Province was 10.575 million, and the number of returning residents was 85,000, which was basically the same as last year, accounting for 14% of the increase in permanent residents that year. According to survey companies, the localization of employees is significant. In the textile cluster of Suncun, Wuhu, Anhui, there are 22,000 employees and 90% local people. The Wangjiang Textile Industry Cluster represents 17,000 employees in the cluster and 85% local people.
The enterprises in Anhui and Jiangxi are mostly processing enterprises. In recent years, they have begun to build brands gradually. Second, there is a shortage of brand operation personnel. Compared with the lack of first-line employees, the lack of brand operations personnel is even more serious. The introduction of talent is difficult, and it is equally difficult to retain talent after the introduction.
The rise of smart manufacturing
With the changes in the social structure of our country's society, most of the newly recruited labor force is only children, and they are reluctant to engage in factory production. Even if they are recruited, they are not willing to work on night shifts. The problem of recruiting workers is becoming more and more obvious. As a result, enterprises are forced to speed up their intelligence. Transformation.
Nearly 3,000 square meters of cutting workshop of Xiamen Wei Da Si Garments Co., Ltd. is exceptionally “empty”, with less than 10 workers. This is due to the fact that the company spent 10 million yuan in October last year to introduce smart clothing manufacturing systems such as automatic cutting machines, intelligent hanging production lines, and intelligent shuttering machines, which have improved production efficiency by more than 30% and product quality has become more standardized.
Zhejiang Hengyi Group's 300 million ton filament project in Haining has an employment quota of 1,200 employees, 800 of whom are senior skilled personnel from the electromechanical profession. The industry's talent structure has changed.
Jiangsu Huafang Group provided a very convincing set of data. Compared with 2006, the Group’s yarn and fabric production capacity and output did not shrink, but the relevant employees have reduced from nearly 40,000 to 11,000 in 2017. .
Jiangsu Yangfan apparel once updated 200 sets of Shimadzu's full-form knitting flat knitting machines. The artificial demand for manufacturing sweaters has been greatly reduced, and the efficiency has been greatly improved.
Wuxi Hengtian Textile Co., Ltd. clothing manufacturing workshop constantly updated the automation of a single process, while going to complex skills, but also trying to make the entire production line intelligent. Hengtian hopes that through scientific and technological strength, the factory's production efficiency will reach 5 to 10 times of 2016 after 5 to 10 years.
In Zhejiang, besides the Annunciation Bird and Zhuang Ji, for most small and medium-sized garment enterprises, the development of smart manufacturing is more inclined to solve corporate real problems rather than blind development. With existing equipment reforms and practicality, investment can significantly improve efficiency. In addition, smart manufacturing reduces labor requirements while reducing the need for artificial proficiency.
Textile and garment companies in Hebei, Hunan, and other places are also actively promoting “intelligent machines” and “intelligent manufacturing” to achieve reductions in staff efficiency. This not only effectively solves the lack of employment, but also eases the pressure of rising labor costs.
Directional cultivation of fiery
In order to stabilize the workforce, many enterprises in Hunan Huarong have raised the wages of workers one after another, and the cost of labor has been higher than that of developed coastal regions. Many companies in the survey emphasized that the people-oriented nature of the industry must be transformed from human-based costs to human-based capital, and that industrial workers are the power of the real economy. Then, how to cultivate qualified industrial workers? How to make up for the “gap between the classroom and the industry?” How to tap the local labor resources?
Most Shaanxi textile enterprises compete for posts and incentives, dig out and cultivate talents that meet the needs of enterprise development, optimize the configuration of posts; take key forms and key positions in various forms to attract talents from the society; focus on the training of grassroots management personnel and professional and technical personnel Enhance the theoretical level and professional skills, enhance scientific and technological research and development, technological innovation and other aspects of capacity; overall arrangements for the functional departments of systematic training; strengthen business knowledge training with daily work, the ideological education, institutional education, skills education organic combination, Continuously improve the overall quality of cadres.
In Tianjin, Shanghai, and other places, textile colleges and universities set up personnel training mechanisms for three-way cooperation among schools, industries, and enterprises in the process of promoting personnel training, scientific research, and social services. For the company to carry out vocational training, for example, from 2014 to 2016 for three consecutive years to Nanshan Group to carry out training, at the same time, Yinchuan more than 30 wool textile companies to come to school for training.
Guangdong, Fujian and other places have also seen the importance of cultivating regional industry reserve talents. They have proposed that talents need to be increased and that they need to revitalize stocks, inject more external fashion master resources through the platform of institutions, and improve students through cooperation mechanisms between production, education and research. Local employment rate. For example, the Guangdong Vocational and Technical College has trained Guangdong Esquel's professional talents for five consecutive years. At present, the most sought-after student of the college is the graduate of the Dyeing and Finishing Technical College. On the one hand, it reflects the employment competitiveness of applied professional talents, and it also reflects the industry's thirst for professional talents.
At the same time, Guangdong, Fujian and other places are also working hard to solve the problems most concerned by front-line workers, such as wages and benefits, work environment, housing for migrant workers, and children’s education issues, etc., and use thoughtful and appropriate supporting services to attract and retain workers. Increase resources support, stabilize management and design talents, make full use of local policy measures and superior resources, and provide supporting services for talents. For example, the construction of fashion supporting projects, the construction of traffic networks and the construction of communities will increase the level of planning and optimize the development environment. Of the more than 4,000 merchants in Guangzhou International Textile City, one-third came from Chaoshan, 20% came from Lingnan, 20% came from Wenzhou, and the rest came from all over the country, which had a significant siphon effect on talents. In particular, the demand for apparel design capabilities, the increasing demand for design talents, the ability to absorb has gradually increased, but also injected new vitality for market development.